When it comes to electrical work, ensuring a reliable and durable connection is crucial. Creating and weatherproofing a wire splice is an essential skill for any DIY enthusiast or professional electrician. This guide will take you through the steps to create a secure wire splice and weatherproof it to withstand the elements, ensuring a long-lasting connection.
Steps to Create a Secure Wire Splice
Choosing the Right Tools and Materials
Before starting, gather the necessary tools and materials:
- Wire strippers
- Electrical tape
- Heat shrink tubing
- Soldering iron and solder
- Waterproof connectors or splice kits
Creating a Wire Splice
While there are numerous types of splice kits and wire connectors available, being able to properly solder wires, and the ability to weatherproof the new splice will save time, money, and frustration. This article will guide you on the right path to learning a new skill by outlining the proper technique to splice wires and create a weatherproof seal to protect outdoor electronics. For individuals who are new to soldering, wire splicing is a basic soldering skill that will definitely come in handy over time.
You will need your soldering tools from the list above.1. Take your wire stripper and strip 3/4 of an inch of the outer insulation from both of the wires you are splicing together.

2. Take a piece of 8mm shrink tube about 3 inches long, and slide it down one side of the wire bundle. (Don't forget this step, or you'll regret it after you've finished the splice.)
3. Once wires are stripped, take a 1/2 inch piece of 3mm Heat Shrink Tubing and place one section over each individual wire.

6. With a hot soldering iron, use the side (not the tip) to heat the wire and melt the flux. The heated flux will evenly pull the melted solder into the wire.

8. Using your heat gun, shrink the tubing, now continue to solder the remaining wires, shrinking each one as you go.
Weatherproofing Your Wire Splice
1. Once all individual wires are soldered and covered with shrink tubing, you can take your clear silicone and run a thin bead over the exposed spliced wires. Take the 8mm shrink tube and slide it over the silicone and wires.

2. Using your heat gun, start shrinking in the center of the tube. As the tube shrinks work out to one side, move back to middle and work out to opposite side. Be careful working from the center out as it pushes the silicone into every gap. The excess silicone will squeeze out of the end, and it can be hot.

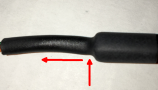

3. Let the silicone cool for a minute. Using your finger, take the excess silicone and coat the entire area making sure to cover where the shrink tubing is and 1 inch past on both sides. You may add more silicone if you feel that there is not enough covering the wire.
Stripping the Wires
Begin by stripping the insulation off the ends of the wires you want to splice. Use a wire stripper to remove about an inch of insulation from each wire, exposing the bare copper. Be careful not to nick or damage the wire strands, as this can weaken the connection.
Twisting the Wires Together
Once the wires are stripped, align them side by side and twist them together tightly. This step ensures a good mechanical connection, which is essential for both electrical conductivity and structural integrity. For optimal results, twist the wires in a clockwise direction, ensuring they are tightly bound.
Soldering the Connection
To create a permanent and reliable connection, solder the twisted wires together. Heat your soldering iron and apply it to the twisted wires, then carefully add solder until it flows into the strands and covers the entire splice. This process creates a strong bond that prevents the wires from coming apart, even under stress or vibration.
Applying Heat Shrink Tubing
Slide a piece of heat shrink tubing over the soldered splice before it cools down completely. The tubing should be long enough to cover the entire splice and a bit of the insulated wire on either side. Use a heat gun to shrink the tubing, which will create a tight seal around the splice. Heat shrink tubing adds an extra layer of insulation and protection, ensuring that the splice is secure.
Weatherproofing the Wire Splice
Using Waterproof Connectors
For outdoor or exposed connections, use waterproof connectors or splice kits. These products are specifically designed to protect electrical connections from moisture, dust, and other environmental factors. Follow the manufacturer’s instructions to ensure a proper seal and reliable protection.
Applying Silicone Sealant
After securing the splice with heat shrink tubing, you can add an extra layer of protection by applying silicone sealant. This step is particularly useful for splices exposed to harsh weather conditions. Spread a thin layer of silicone sealant over the splice and the surrounding wire insulation, ensuring that all gaps and openings are covered. Allow the sealant to cure according to the manufacturer’s instructions before exposing the splice to the elements.
Wrapping with Electrical Tape
For additional protection, wrap the splice with high-quality electrical tape. Start a few inches away from the splice and overlap each layer as you wrap, covering the entire splice and extending onto the insulated wire. Electrical tape adds another layer of insulation and helps to keep moisture and debris out of the splice.
Testing the Connection
After creating and weatherproofing your wire splice, it’s essential to test the connection to ensure it is working correctly. Use a multimeter to check for continuity and verify that the splice is conducting electricity as expected. This step helps to confirm that your splice is secure and ready for use.
Please, contact our technical support team if you need any additional help or have any questions about soldering or desoldering. We are always happy to help.